What is MSI?
How Multi-Sensor Inspection increases safety while saving time and money
Pipeline infrastructure is critical to the health and wellbeing of a community, whether it is wastewater or stormwater. The reliability and safety of these pipelines are critical to avoid potential disasters, and yet inspection, maintenance, and repair are often underfunded or ignored.
If maintaining pipeline integrity is so important, why is it often ignored until there is an emergency? Preventive maintenance is often overlooked when cities and towns don’t understand how easy and cost-effect inspection techniques have become.
Old or “traditional” inspections methods face several barriers:
- Pipelines can be hard to access
- Manual inspection is unsafe and time consuming
- Lack of technology to store and interpret findings
Multi-sensor inspection (MSI) overcomes these barriers. MSI uses various inspection techniques to identify defects and potential problems in pipelines in a safe and cost-effective manner. This ebook will provide an overview of MSI for pipes, including the different techniques used and their benefits.
Introduction to Multi-Sensor Inspection
Multi-sensor inspection is a comprehensive approach to inspecting pipelines. It involves combining multiple inspection techniques to obtain a more accurate and detailed assessment of a pipeline’s condition. These techniques can include visual inspection, magnetic flux leakage (MFL), ultrasonic testing, and radiographic testing. MSI is critical for ensuring the safety and integrity of pipelines, as it can detect defects that may be missed by a single inspection method.
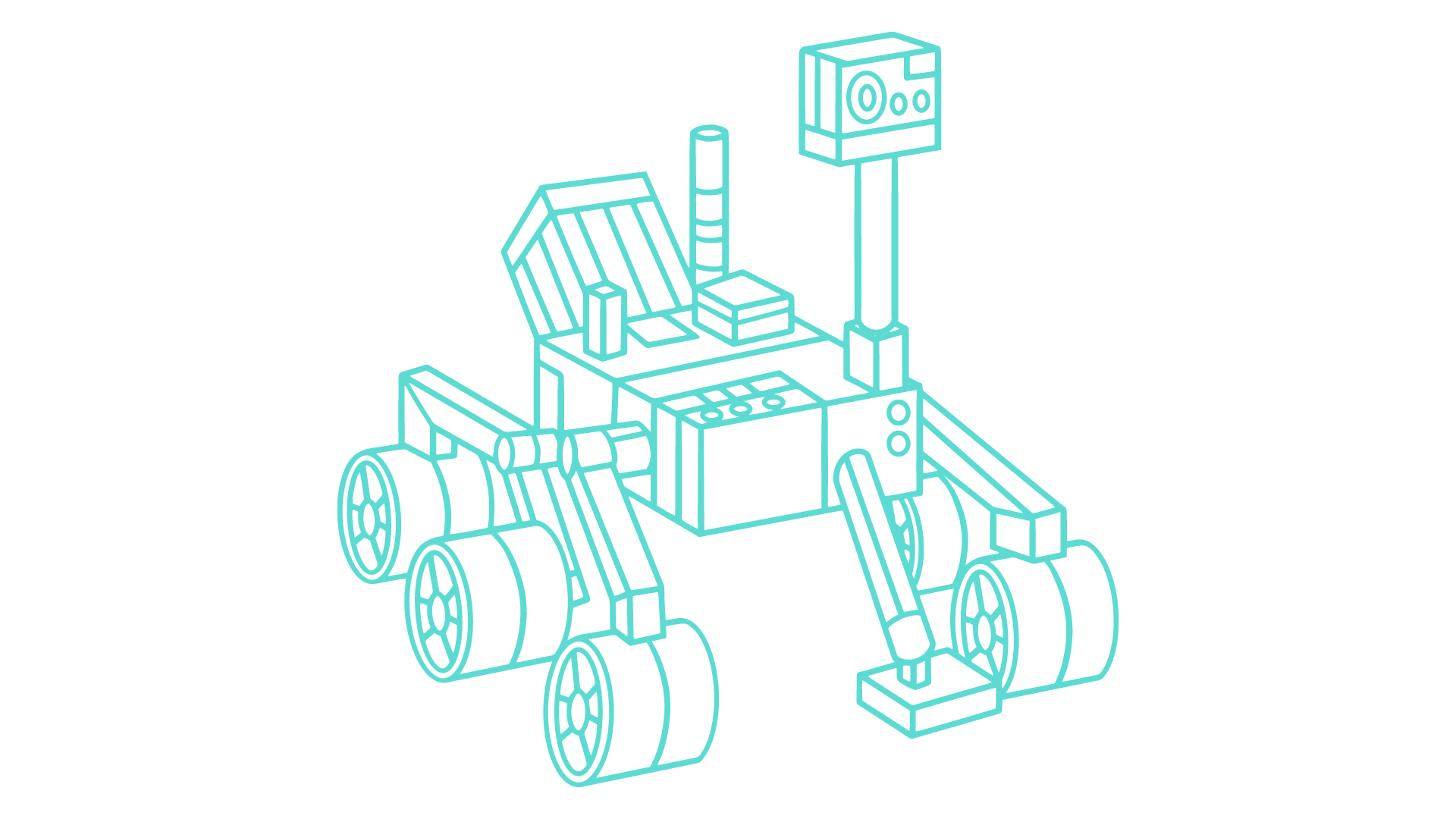
Visual Inspection
Visual inspection is the most basic form of inspection and involves visually examining the pipeline. For hard-to-examine pipelines, forward-thinking municipalities are beginning to use drones to access and transmit video of the conditions. Visual inspection is often the first step in MSI and can be performed by trained personnel to identify many surface-level defects such as corrosion, dents, and cracks. For increased speed and accuracy, Artificial Intelligence (AI) can be used to accelerate visual data analysis. Visual inspections are useful in identifying defects that may require further inspection using additional techniques.
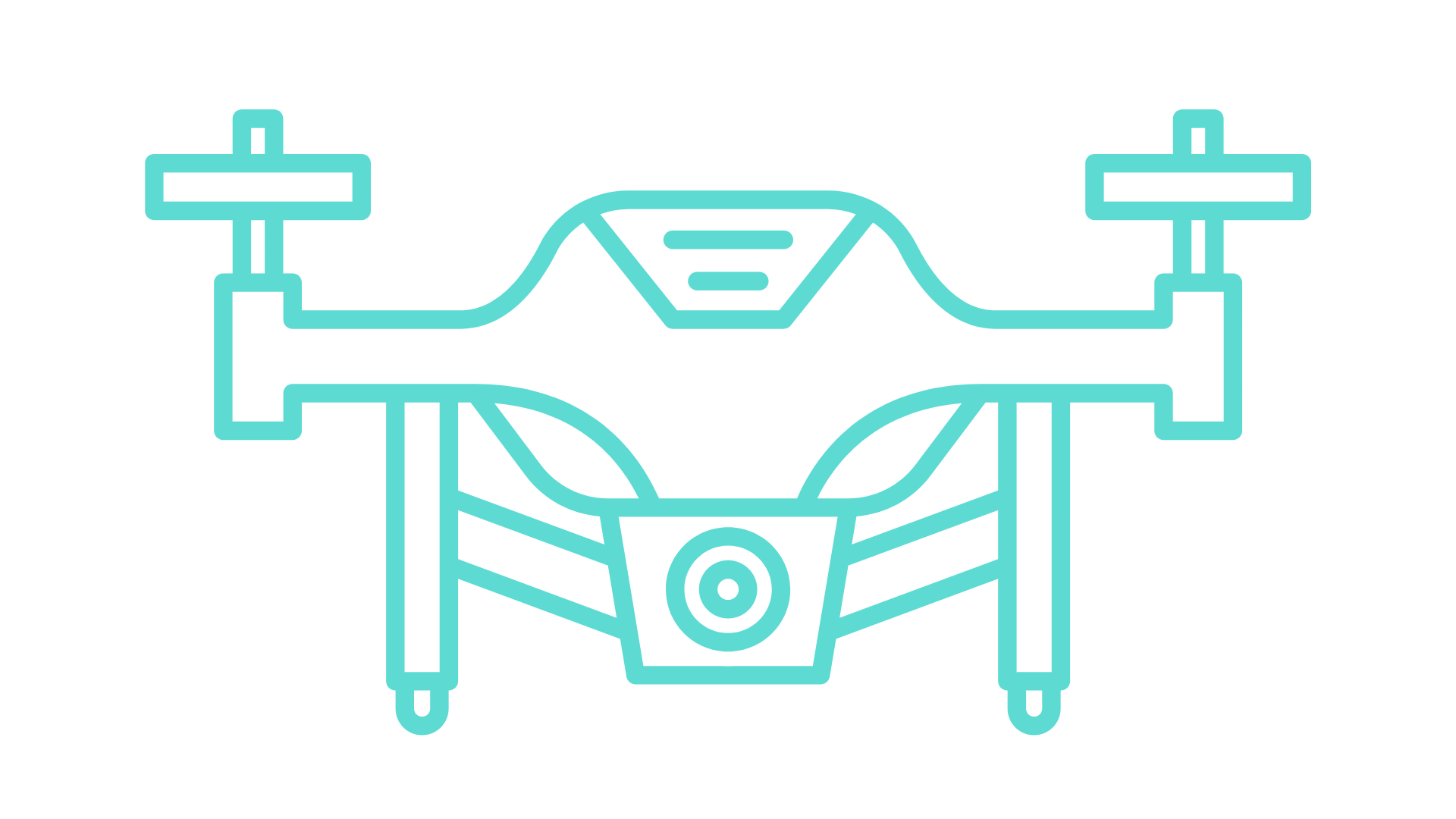
Magnetic Flux Leakage (MFL)
Magnetic flux leakage (MFL) is a non-destructive testing technique that uses magnetic fields to detect defects in pipelines. The technique involves running a tool through the pipeline that generates a magnetic field. Any defects in the pipeline will cause a leakage of magnetic flux, which is detected by sensors in the tool. MFL is useful in identifying defects such as metal loss, corrosion, and pitting.
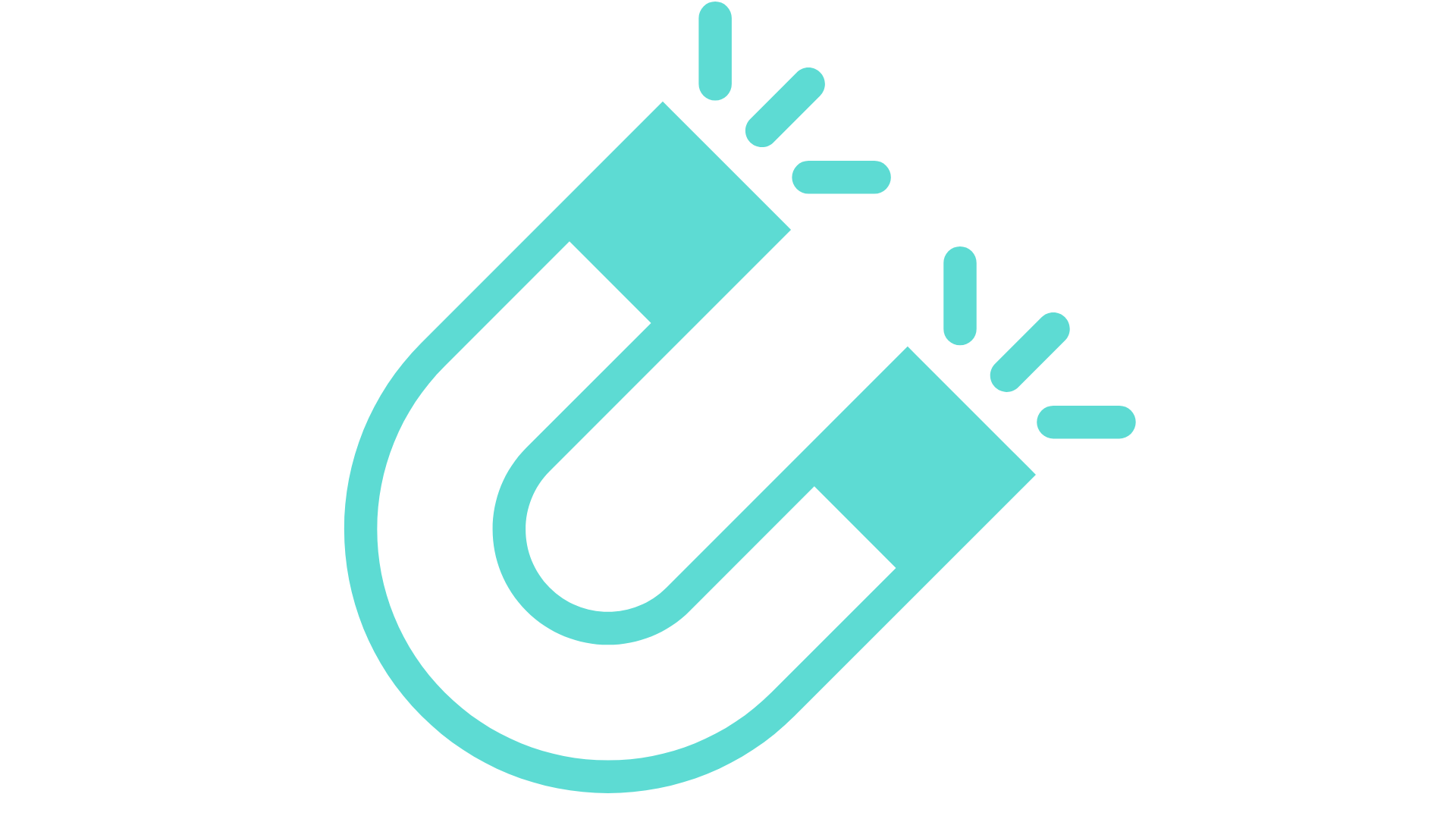
Ultrasonic Testing
Magnetic flux leakage (MFL) is a non-destructive testing technique that uses magnetic fields to detect defects in pipelines. The technique involves running a tool through the pipeline that generates a magnetic field. Any defects in the pipeline will cause a leakage of magnetic flux, which is detected by sensors in the tool. MFL is useful in identifying defects such as metal loss, corrosion, and pitting.
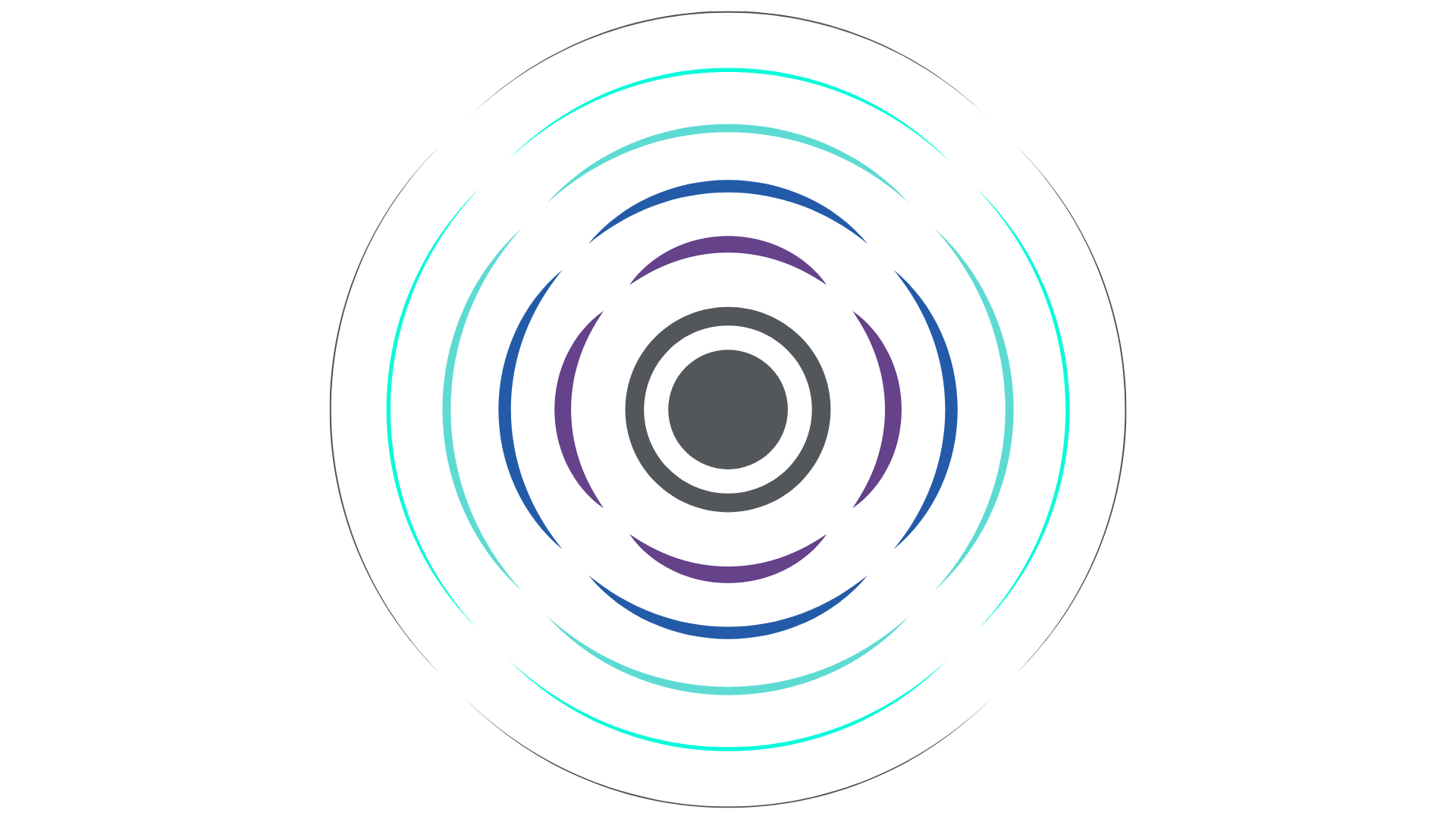
Pressure & Temperature Sensors
Pressure and Thermal sensors perform a critical role in pipeline inspection and maintenance efforts. Variations in either pressure of temperature can be early warning signs of defects and help inspections to quickly detect and localize risk areas and leaks
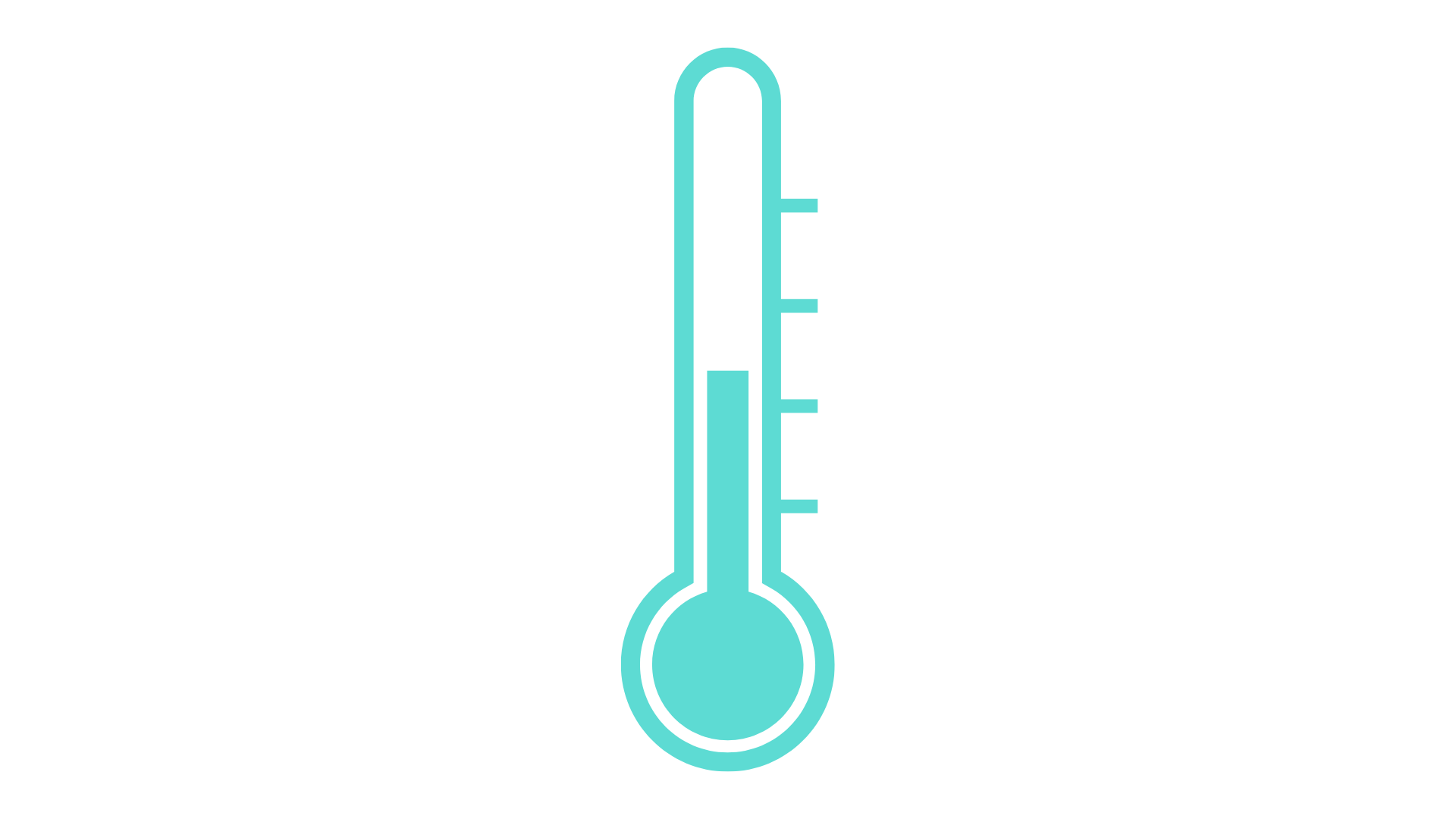
Benefits of Multi-Sensor Inspection
The benefits of multi-sensor inspection for pipes are significant, especially when paired with automated data analysis. By combining different inspection techniques, MSI provides a more accurate and comprehensive assessment of the pipeline’s condition. Automated analysis accelerates reporting on pipeline conditions and helps prioritize areas that need attention. This approach can detect defects that may be missed by a single inspection method, increasing the overall reliability and safety of the pipeline. Additionally, MSI can reduce the need for costly repairs and minimize downtime for maintenance.
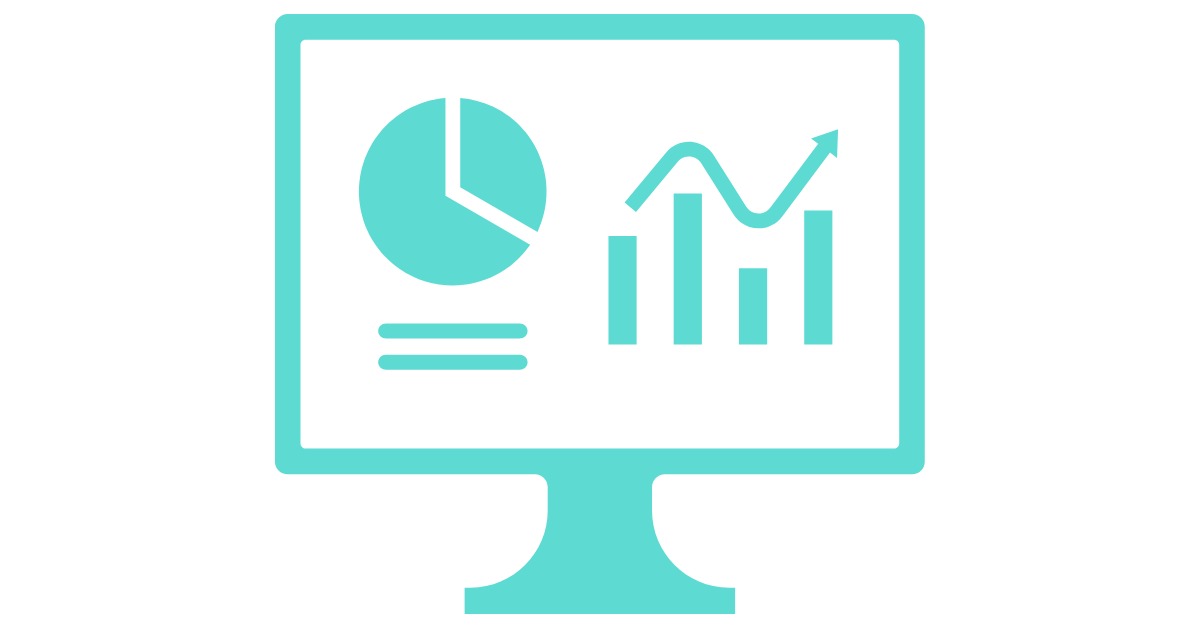
Choosing the Right Sensors for your Pipeline
The correct sensor arrays depend on the design of your pipeline. Consider:
- What material is the pipeline made of?
- What does the pipeline carry?
- Where does the pipeline run?
- What is the age of the pipeline?
It is often helpful to work with inspection experts to determine the right combination of sensors that will provide the accurate data you need, and that the chosen hardware is robust enough for the unique conditions of your system.
Making Sense of Sensor Data with Automated Analysis
The correct sensor arrays depend on the design of your pipeline. Consider:
- What materials is the pipeline made of?
- What does the pipeline carry?
- Where does the pipeline run?
- What is the age of the pipeline?
It is often helpful to work with inspection experts to determine the right combination of sensors that will provide the accurate data you need, and that the chosen hardware is robust enough for the unique conditions of your system.
Conclusion
Multi-sensor inspection for pipes is critical for ensuring the safety and integrity of pipelines. The right combination of sensors may combine visual inspection, MFL, ultrasonic testing, thermographic, and/or pressure testing, to provide a comprehensive assessment of the pipeline’s condition. This approach detects defects that would be missed by traditional inspection methods and increases the overall reliability and safety of the pipeline. With MSI, pipeline operators can reduce the need for costly repairs and minimize downtime for maintenance, ultimately resulting in improved efficiency and safety.